
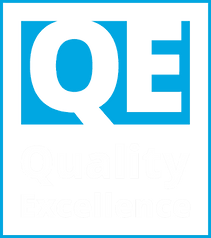
A.A.S. Quality Journey
Our quality journey starts from an idea and never ends
The drip irrigation solutions that we provide, either production lines, emitters or services, are designed and developed by our team of experts with one priority, to add value to our partners. We believe that in order for a product to be able to add value, it has to be produced with the highest quality standards, in every step of the process, from design and production to delivery, training and after sales support.
​
To achieve and maintain our high-quality standards, we have developed the Quality Excellence process. This process enables us to constantly offer drip irrigation solutions of the highest quality, since we never stop evolving our design, development and production processes, which enhance our product portfolio. We put to the test all our ideas no matter how bold or complex may seem, in order to convert them into the optimum possible solution for our partners.

Unique Product Design
All our products start their life cycle at the R&D department, which is constantly designing and developing drip irrigation solutions. Furthermore, since we are a company striving for excellence, we have established two additional active channels for product development.
​
-
The internal, where our team of experts is constantly developing the product portfolio and finds ways to enhance the offered solutions.
-
The external, where the marketing and sales departments join forces for developing strategies that will address specific market needs in a form of a product.
​
Both channels end up to our R&D department for a feasibility study and upon their approval, the ideas are transformed to a product design.
Emitter design
​
Our emitters are designed with three main characteristics, high performance, durability and cost effectiveness. In order to combine those three elements, we utilize the most advanced 3D Computational Fluid Dynamics Simulation “CFD” for their design. A technology used in multiple industries nowadays, originally developed for the aircraft industry and used for airplane design. CFD enables our emitter design team to calculate with extreme precision many critical values and features that determine the quality characteristics and accuracy of our emitters. From the moment the water enters the filtration area until the time that will reach the outlet of the dripline. Moreover, CFD provides valuable data for the water velocity and pressure inside the flow path of the emitter. The data are used for determining the flow in l/h and fine tuning the design in order to enhance the clogging characteristics of the emitter.
Aquarius PC Emitter
Especially for the PC emitters where the use of CFD is extremely complicated and requires advanced skills, the knowledge, experience and expertise or our team is a key factor for success. This is the reason why we have developed proprietary CFD models for all our PC emitters.
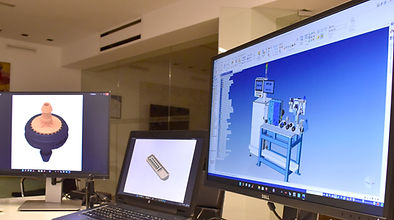
The first thing that the design team addresses is the total mass of the emitter, since the product except from functional it has to also be cost effective. Starting from the water flow around the emitter while into the dripline, we calculate the friction coefficient (Kd) which is the pressure loss caused by the emitter. The total filtration area of the emitter is the second element and a very critical one, since it’s the first anti clogging mechanism of the emitter. Depending on the design, the inlet area of the water into the emitter is in some cases the actual filtration mechanism.
The next function calculated with CFD is the water velocity inside the labyrinth that will determine the flow in liters (or gallons) per hour. The most important use of CFD by far in the emitter design process, is the actual turbulent flow of water inside its labyrinth. The turbulent flow is the most important anticlogging mechanism of the emitter. Every fine particle that has passed through main and emitter filtration, will also pass from the labyrinth due to the turbulent flow and therefore the emitter will not clog.
Production line design
​
All individual parts of our production lines are designed in-house and manufactured from carefully selected suppliers, according to our specifications under proprietary mechanical designs. A.A.S. production lines are designed for the optimal and uninterrupted operation, at the highest possible production speed, with the maximum efficiency. Our dedicated R&D department is constantly upgrading every single part, using the latest technologies in every element, in order to offer the most efficient production lines of the highest quality that will add value to our partners production.
​
Another design feature which although is not visible, it’s one of the most important elements of our production lines nowadays, is the fully customized in-house developed operation software. The software of our production lines is designed from the dedicated R&D team and makes all parts work together in perfect harmony for the highest efficiency and effectiveness. Additionally, our team has designed easy to comprehend and operate interfaces, that require the minimum effort from the line operator, in order to perform even the most complex task with ease, on several parts of the production line.
N350 FL Production Line
Uncompromising Supplier Selection
Being a manufacturing company, we work with several suppliers that provide a wide variety of products and raw materials for both our operations and production. Therefore, the careful selection of our suppliers is crucial for both the products we provide to our partners and the seamless operation of our company. By constantly evaluating all suppliers with dedicated procedures for each sector, operation and product, we monitor the quality of their offerings and so we are able to provide to our partners quality excellence.
All the machines used for our emitter production are state of the art, top of the range models from each supplier. From the injection molding machines and the cavities used, to the assembly and quality control testing, they are all selected with one priority in mind, and this is the highest possible quality for our emitter production.
The companies that supply the individual parts of our production lines, are long term associates who have proven their qualities, capabilities and loyalty. Moreover, they are always ready to constantly push the boundaries with our innovative ideas and designs. We know that all the designs that leave our premises are safe and all parts that we will receive will be manufactures according to our exact specifications. Nonetheless, we have set dedicated inspection procedures for every single part, in order to be tested thoroughly before it reaches our partner’s production facility.

The raw materials used in emitter production are equally important as the design of the emitter. We are very keen on raw material quality and supplier selection, since it’s the vital ingredient of the emitter performance, quality, chemical and UV resistance and of course durability. A common struggle in pressure compensating emitter production is the selection of the silicon membrane and its consistency. We have eliminated this problem by developing a unique in the industry procedure which has several steps in receiving the desired specifications.
Advanced Production and Assembly Procedures
All our production procedures are developed to promote quality over cost. The automations and technologies that we use are the latest available in the industry and enable us to control our product’s quality in every step of the process, either production or assembly.
Moreover, we have adopted several ideas and procedures from different industries in order to enhance our production processes and capabilities with a positive overall result in both the efficiency and quality. We are proud to be the industry pioneers in adapting the latest developments in our procedures.
State of the Art Production Lines
We constantly invest in new production lines and equipment in order to provide high quality solutions to our partners, while at the same time increase effectiveness and efficiency. Our emitter injection molding machines are the most advanced in the industry and perfectly maintained in order for them to operate in the most effective and efficient way. Our assembly machines used for assembling the pressure compensated (PC) emitters are state of the art, using the latest technology that the industry offers. They incorporate custom laser or ultrasonic welding technology depending on the emitter characteristics.
​
Moreover, all our injection molding and assembly machines are constantly upgraded, both in terms of hardware and software, with the latest available options. We want to remain the global leader in our field of expertise in every possible aspect, in order to constantly add value to our partners.
Utilization of New Technologies
We are proud to be the early adopters in the industry, since we put to the test every new technology available for both our products and production procedures. By this way we add value to our operations that passes to our partners through our offered products and gives us the edge in the industry. Our R&D department enables us to achieve that, by perform all necessary test and optimize the use of new technologies in every area possible.
​
Our latest development is the Artificial Intelligence (AI) integration in our flat production lines. We are the first company introducing AI in the drip irrigation production industry.
​
Another example of innovation is our Cyclone PC emitter, which utilizes state of the art, laser welding technology for sealing the two parts of the emitter. This unique feature ensures quality excellence of the emitter, the lowest possible CV and its flawless operation under any condition.
​
Software development is another very important aspect of our quality excellence in many operations. For example, it plays a drastic role in achieving the high efficiency and industry leading production speeds of our production lines.
​
Finally, we use the new technologies for providing environmentally friendly solutions to our partners in every possible aspect. From reduced energy, water and consumables to optimal production procedures to reduce their scrap to the minimum possible.
Cyclone PC Emitter
Specialized, Highly Trained Employees

In our constant effort for quality excellence, we rely on our most valuable asset, our employees. Every team member is a highly trained professional in its field, who constantly adds value to our operations. We strongly believe that the best investment in our company is the one in human resources and we practice our believes by employing highly skilled employees with proven track record in their field of expertise and creating a safe, healthy and environmentally conscious work space for everyone.
We all strive for excellence and constant improvement in everything we do. Under this scope, we pass all our knowledge, experience and expertise to our partners via the offered drip irrigation solutions, either products or services.
Ideal Production and Climatic Conditions
The climatic conditions play a significant role in emitter production and assembly and therefore their overall quality. We keep our facilities in a specific temperature and humidity range, in order to optimize the production and ensure our quality standards.
​
Moreover, we make sure that our production floor is extremely clean in order to prevent foreign particles and dust from entering our injection and assembly machines. Every door that leads to the production or assembly floor is sealed, in order to keep the dust away from our production lines and equipment.

We are so committed in emitter quality and determined to offer the higher industry standards that we have taken emitter production procedures to the next level. For instance, our factory employees never touch with naked hands the emitters, in order to prevent any kind of dirt, particle or contamination to enter their labyrinth.
Specific Packaging Materials and Procedure
Emitter packaging is crucial in maintaining their quality and characteristics. The boxes used are carefully selected and laid with a thick membrane in order to keep the dust away. Moreover, after each box is sealed, the whole pallet is wrapped several times with film in order to keep the emitters in top order, for both storing and shipping conditions.
​
Packaging of the emitters is performed in the clean area of the production floor, in order to prevent dust entering the emitter boxes. The packaging materials used are carefully selected in order to keep the emitters clean and prevent any contamination.
Perfect Storing Conditions
Our dedicated emitter storehouse is situated next to production. This means that as soon as a pallet is ready from production, the operator opens the automatic door and places the pallet directly in the wrapping machine in order to seal the products. The storehouse is designed to accommodate only the emitters and it is used for a short time period.

Strict Quality Control

Our quality control procedures and testing are performed by a dedicated team, under the strict supervision of both production and R&D departments. We have set in place strict quality control checks in all production phases by using the latest technology available. Moreover, the quality control team is constantly checking the emitters by taking samples from all production phases, to ensure that all products are within the described specifications and maintain their characteristics. By enforcing all those quality processes and control phases, we have managed to minimize and eventually eliminate production defects.
Α similar quality control process with several phases is also in place for our production lines. Every individual component is thoroughly inspected and tested in our dedicated production line test facility, during installation in its predetermined position and at the final assembly stage, for the complete production line operation test. Each production line that we offer, passes the thorough quality, performance and safety tests in our facilities. The final step is to produce adequate quantity of dripline according to the specifications prescribed.

Moreover, we provide a unique opportunity to our partners, to visit our facilities and inspect in person their production line operation, before packing and send it for commissioning in their premises. This strict quality control procedure, guarantees that every line is shipped and delivered fully functional and safe to our customer.
ISO Certification
Although we were working under very strict processes from the first day we started to operate, on 2020 we have received ISO 9001:2015 standard certification for our operations. Moreover, all our emitters surpass the ISO 9261 standards since are produced with extremely lower tolerances than the ones required to achieve the certification. Although ISO 9261, is the only recognized certification valid worldwide for drip irrigation, there are far more strict local certifications in many different countries that our emitters comply with.
​
In addition to the internal design and testing protocols, we follow very strict and safety standards, for both our own production but also for the production lines and machinery that we offer. More specifically we comply to ISO 12001 acoustics standard, which specifies the technical requirements of a noise for machinery and equipment. Moreover, we comply to IEC 60204 safety standard, which commences at the point of connection of the supply to the electrical equipment of the machine and applies to electrical, electronic equipment and machines, working together in a coordinated manner. Finally, all our products carry the CE marking since they conform to the highest European and International standards for health, safety, and environmental protection.
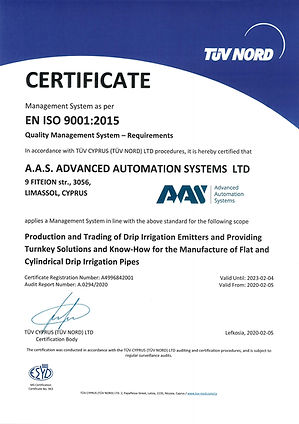

Advanced Maintenance of Production Lines and Equipment
The correct and regular maintenance of all production machines and equipment is vital for emitter production. A poorly maintained injection molding machine can have a huge impact on the flow rate, clogging and overall performance of the emitter. In most of the cases the results are only visible on the field, when it is too late to take corrective actions since the farmers have already faced severe crop and income loss.
​
This is the reason why we have set periodic maintenance procedures, which are tailored to each production machine. Additionally, instead of pushing back maintenance in favor of production, or performing all maintenance during the down and vacation period, we prefer to hold a larger emitter stock and follow a strict maintenance timetable that will keep our machinery in perfect operating conditions. Moreover, we have put in force additional quality control procedures during emitter production, which ensure the quality excellence of our emitters.

By utilizing our experience in emitter production, we have developed a unique maintenance procedure for our molds, on top of the ordinary manufacturer’s standards. Our experience has shown that over time the mold’s cavities need a specific treatment in order for them to maintain their characteristics. This is extremely important in drip irrigation products since the cavities determine the emitter flow and their anticlogging characteristics. Their tolerance has to be extremely low in order to achieve an equally low coefficient of variation (CV) and therefore an exceptional emitter.
Constant Upgrade of our Products and Software
In order to achieve the quality excellence that we praise, we never stop evolving. We believe that there is always room for improvement in both products and services. The very fast pace of technology evolution enables us to utilize it in every possible way in order to constantly provide improved and environmentally friendly, drip irrigation solutions.
​
This is why we constantly strive for improvement in every aspect of our operations. Either it’s a development that will improve our production and our partners will never get to experience, or a product upgrade that will provide a solution to their needs, we will take that step to deliver the best possible solution and add value to our partners.
Long Term Partnerships with the Top Companies
in Drip Irrigation Industry
The top manufacturers of drip irrigation products worldwide, are among our partners. They trust our production lines and emitters for producing high quality driplines. The production lines that we offer are fully customizable to accommodate both a broad but also the specific market and regional needs. Our emitter’s quality and performance is at the highest level in the market worldwide. They are tested and rated with the highest score by the most recognized interdependent bodies worldwide, Center for Irrigation Technology (CIT) in Fresno California and INRAE, National Institute for Research in Agriculture, Food and the Environment, (former IRSTEA) in France, for clogging and emission uniformity.
Our quality excellence enabled us to achieve long lasting partnerships with globally renowned drip irrigation producers. We provide to our partners the opportunity to produce the highest quality driplines in their region, by utilizing our drip irrigation solutions, our knowledge, experience and expertise.
Global Footprint